The Scientific Research Behind Porosity: A Comprehensive Guide for Welders and Fabricators
Comprehending the elaborate devices behind porosity in welding is important for welders and fabricators striving for flawless workmanship. From the composition of the base products to the ins and outs of the welding process itself, a plethora of variables conspire to either aggravate or reduce the visibility of porosity.
Recognizing Porosity in Welding
FIRST SENTENCE:
Assessment of porosity in welding reveals important understandings into the stability and high quality of the weld joint. Porosity, defined by the existence of cavities or spaces within the weld steel, is an usual concern in welding processes. These spaces, otherwise effectively attended to, can endanger the structural stability and mechanical buildings of the weld, bring about prospective failings in the ended up product.

To identify and evaluate porosity, non-destructive testing techniques such as ultrasonic testing or X-ray assessment are typically employed. These methods permit the recognition of internal problems without compromising the honesty of the weld. By evaluating the size, form, and circulation of porosity within a weld, welders can make educated choices to boost their welding processes and attain sounder weld joints.
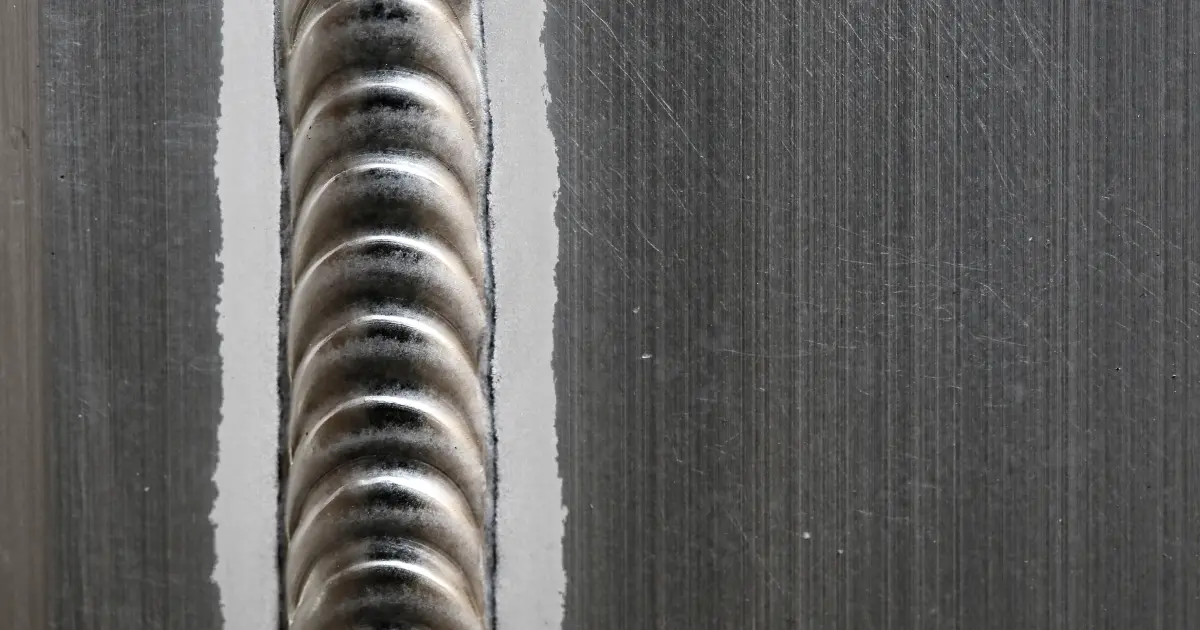
Aspects Affecting Porosity Development
The incident of porosity in welding is affected by a myriad of factors, ranging from gas shielding efficiency to the intricacies of welding criterion settings. Welding parameters, consisting of voltage, existing, travel speed, and electrode type, additionally influence porosity development. The welding method utilized, such as gas metal arc welding (GMAW) or shielded steel arc welding (SMAW), can influence porosity formation due to variations in warmth circulation and gas insurance coverage - What is Porosity.
Impacts of Porosity on Weld High Quality
Porosity formation considerably jeopardizes the structural integrity and mechanical residential properties of bonded joints. When porosity is existing in a weld, it produces voids or tooth cavities within the material, lowering the overall strength of the joint. These spaces work as stress and anxiety focus points, making the weld more prone to cracking and failing under load. The existence of porosity also weakens the weld's resistance to rust, as the entraped air or gases within deep spaces can respond with the surrounding setting, resulting in degradation over time. Furthermore, porosity check that can prevent the weld's capacity to stand up to stress or influence, more endangering the total quality and reliability of the welded structure. In important applications such as aerospace, automotive, or structural building and constructions, where safety and security and toughness are extremely important, the detrimental impacts of porosity on weld top quality can have serious consequences, highlighting you can try here the significance of lessening porosity through correct welding methods and procedures.
Methods to Reduce Porosity
Additionally, making use of the appropriate welding specifications, such as the proper voltage, existing, and travel rate, is critical in preventing porosity. Maintaining a regular arc size and angle during welding additionally helps decrease the probability of porosity.

Moreover, selecting the ideal securing gas and preserving proper gas flow prices are essential in lessening porosity. Using the ideal welding method, such as back-stepping or using a weaving motion, can likewise help disperse warmth uniformly and reduce the opportunities of porosity formation. Ensuring proper ventilation in the welding environment to get rid of any kind of prospective sources of contamination is vital for attaining porosity-free welds. By executing these techniques, welders can effectively decrease porosity and create top notch bonded joints.
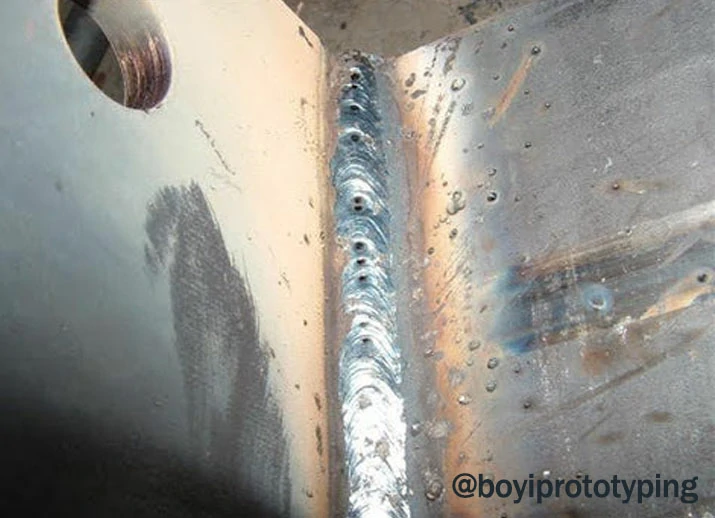
Advanced Solutions for Porosity Control
Applying cutting-edge innovations and cutting-edge techniques plays a crucial duty in achieving remarkable control over porosity in welding processes. Additionally, using innovative welding methods such as pulsed MIG welding or changed ambience welding can additionally aid reduce porosity concerns.
An additional advanced service includes the use of sophisticated welding tools. Making use of equipment with integrated functions like waveform control and advanced power sources can enhance weld top quality and lower porosity threats. Furthermore, the execution of automated welding systems with accurate control over criteria can substantially minimize porosity issues.
Furthermore, incorporating advanced surveillance and examination modern technologies such as real-time X-ray imaging or automated ultrasonic screening can aid in identifying porosity early in the Visit Your URL welding process, permitting prompt restorative actions. Generally, integrating these sophisticated options can significantly improve porosity control and enhance the total top quality of welded components.
Final Thought
In conclusion, recognizing the scientific research behind porosity in welding is important for welders and fabricators to generate top quality welds - What is Porosity. Advanced remedies for porosity control can better enhance the welding procedure and make sure a solid and reputable weld.
Comments on “What is Porosity in Welding: Usual Sources and Efficient Remedies”